Surface treatments –
for all cases
Corrosion protection
Functional or decorative galvanic surface coatings? Zinc coatings? We are the right address!
Functional surface refinement improves the properties of the surfaces of a component in terms of corrosion or wear protection, or improves their electrical conductivity or the reduction of friction forces.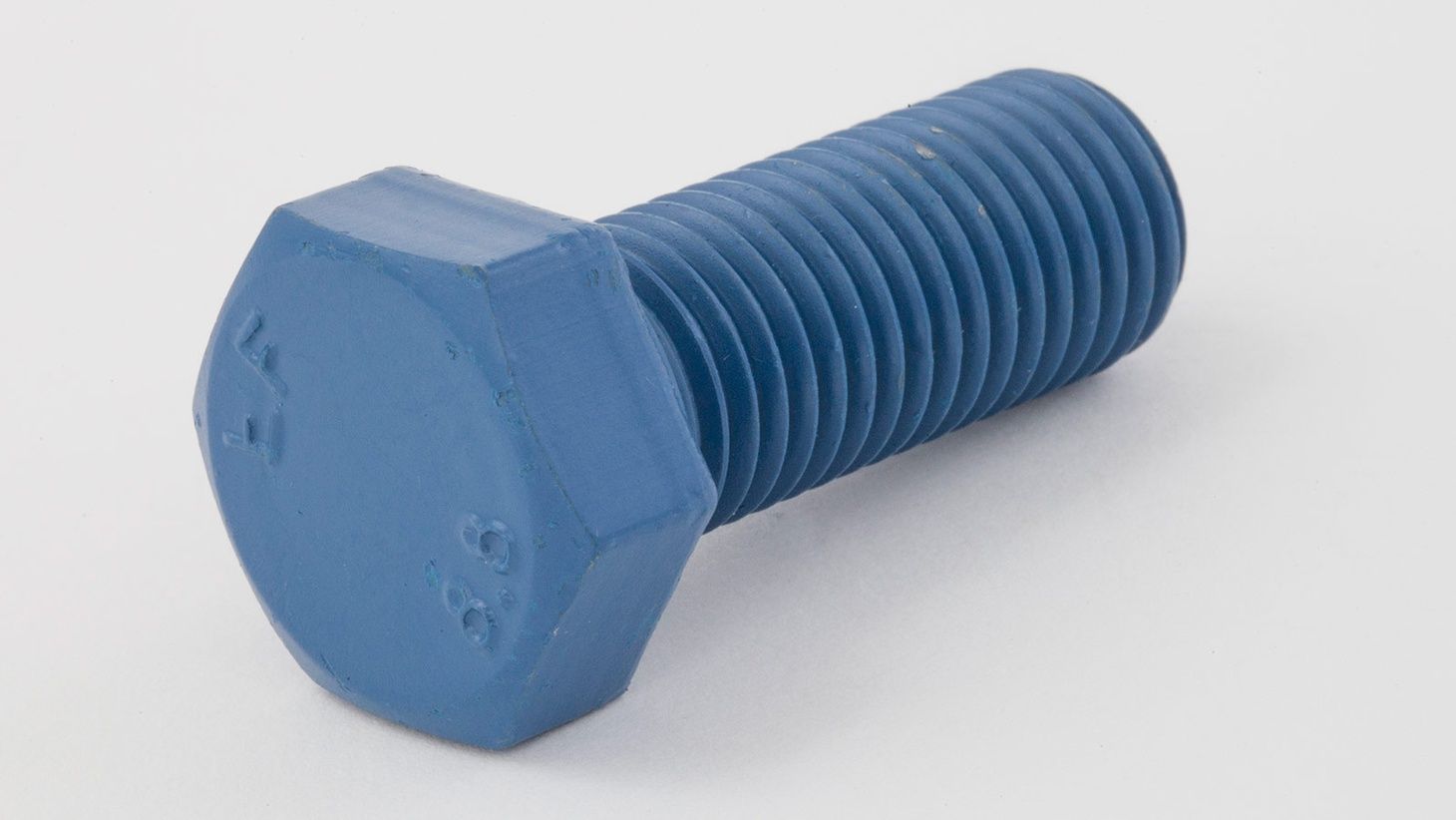
Our range of services includes, for example, the following finishes:
- Phosphating: Zinc or manganese phosphating to ensure improved adhesion of subsequent coatings or to improve slip properties
- Galvanising: Chromated or passivated CrVI-free zinc coatings to produce a temperature-resistant, visually attractive, economical corrosion protection
- Zinc-iron deposition: Black chromated or black passivated CrVI-free zinc coatings to produce a visually attractive, economical corrosion protection with uniform layer thicknesses
- Zinc-nickel coating: Passivated CrVI-free or lubricated or sealed components with uniform layer thicknesses and maximum corrosion protection
- Zinc lamella coating: CrVI-free corrosion protection with thinnest layers and highest corrosion and temperature resistance, consisting of a mixture of aluminium base coats, which are combined with zinc top coats in an inorganic matrix, also suitable for high-strength fasteners of property classes 10.9 and 12.9
Further surface treatment options
- KTL
- Delta Tone, Delta Seal
- Phosphatisation
- Geomet
- Delta
- MAGNI
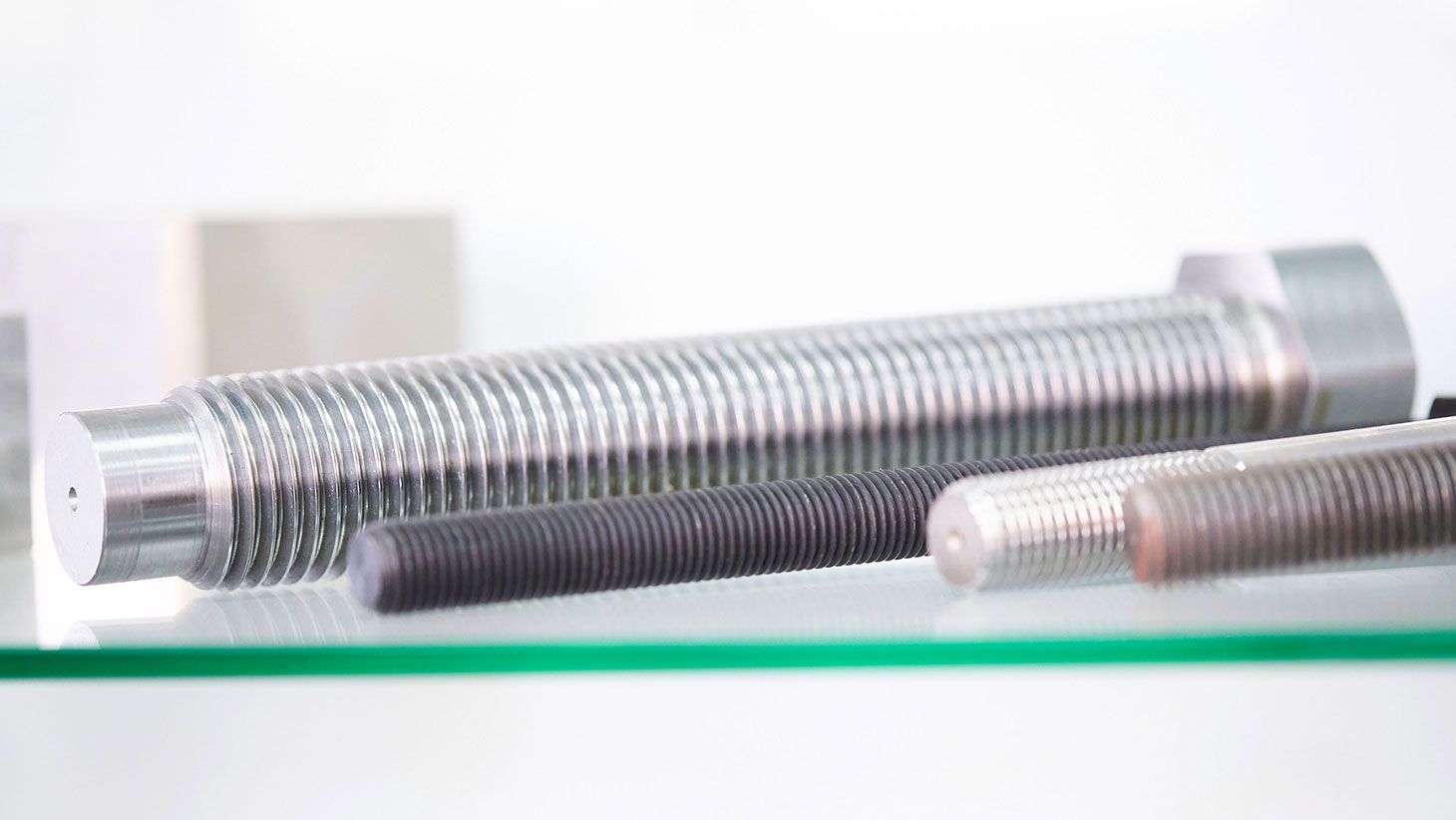
Threadlocks
Under dynamic loads, screw connections tend to come loose automatically. If there is lifting of the frictional locking between the head and support and in the thread, a corresponding coating helps.
If constructive measures to maintain the pre-tension force are no longer sufficient, we recommend that you use the anti-rotation locks for thread locking applied by us as spot or 360° coatings. Our technical consulting is happy to help with the right choice.
The range of services we offer includes the following thread-locking coatings:
- Adhesive anti-rotation locks: according to DIN 267, Part 27, which prevent the automatic loosening of screw connections through the use of micro-encapsulated adhesives. This is provided by polymerisation during tightening to achieve a cohesive connection between the bolt and the nut thread and counteract loosening using a defined torque between the fasteners of an independent loosening.
- Clamping securing devices: according to DIN 267, Part 28, prevent partial loosening of screw connections, but avoid a complete loss of the fasteners. For coating, a choice is made for a range of different polyamides which increase the surface pressure or the frictional engagement on the thread sides, thereby achieving a clamping effect.
The following advantages are achieved through the use of thread-locking surface coatings:
- Avoidance of handling and assembly of additional mechanical safety elements such as nuts or washers, and double storage of these elements
- Layers applied using reproducible processes, which ensure easier and safer assembly, as well as defined process reliability
- Thread-locking surface coatings have high resistance to oils, greases and other chemicals
- The ready-to-use surface coating is dry and non-abrasive, as well as a captive component of the connecting element
Surface
Surface coating that leaves nothing to be desired.
Our customers receive any surface they want. We are proud of that and have been working on it for a long time. Within our network of German partners, many of them from the region, there is no procedure that we have not mastered.And since we know that this high standard has to be checked again and again, every MAX MOTHES partner is audited regularly.
Not only does this enable us to take advantage of our location, more importantly, our network enables us to offer different variations of surface treatments for prototypes and trials (for example, differently set clamping moments for micro-encapsulated plastic coatings).
Documentation
It comes down to the right documentation.
Anyone can create initial sample test reports. We go further: for customer projects, we create CAD drawings that are individually designed. This way, the customer can be sure that we always deliver consistently good quality regardless of geometry, surface or material.Of course, we also take documentation in goods dispatch. In addition, and if necessary, we like to test our products with magnetic powder, dye penetrant or ultrasonic testing for the smallest cracks that are not visible to the naked eye.
Our deliveries are typically done with acceptance test certificates according to 3.1 of EN 10204, meaning we test in-house. For many customers with sensitive products, we are also happy to deliver with a test certificate to 3.2, meaning that external inspectors such as TÜV do the testing.